Melt blown fabric is the most popular non-woven fabric today. Due to the covid-19 pandemic situation, the melt blown manufacturing process is getting popular with increasing medical grade fabric needs. In the previous, we did a detailed discussion about Meltblown nonwoven fabric. In this context, we will talk about the melt blown fabric manufacturing process.
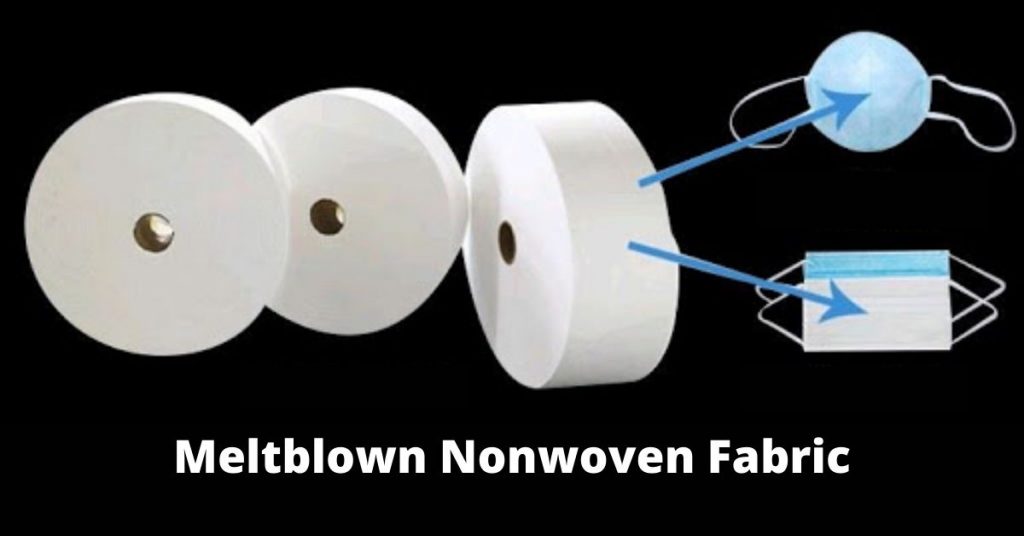
Melt Blown Fabric Manufacturing Process Flowchart:
The melt blow technique forms highly fibrous and self-bonding web by blowing molten thermoplastic resin from an extruder die tip onto a conveyor or take-up screen with high-velocity airflow. The melt blown web’s threads are woven together using a mix of entanglement and constructive sticking. Melt blown fabric manufacturing process by following steps:
- Extruder
- Metering Pumps
- Die assembly
- Web Formation
- Winding
- Bonding
- Finishing

Step-01: Extruder
The extruder is the first step in the production of Melt Blown Fabric. In this step, the polymer granules are placed in the extruder hopper. Rotation of the screws in the heated barrel causes the polymer granules to melt and the barrel screw split into feed, transition, and metering zones. The feed zone is then conveyed to the molten polymer conversion zone through a deep screw channel.
In the conversion zone, the molten polymer is compressed and simultaneously. The molten polymer is then discharged into the metering zone. It serves to create the maximum pressure for extrusion. The force of the molten polymer is highest at this time. Screen packs and breaker plates filter out dirt and infected polymers. The pressurized molten polymer is then delivered to the metering pump.
Step-02: Metering Pumps
The metering pump is a constant-volume, positive-displacement device. This guarantees that the clean polymer mixture flows continuously through different processes, including viscosity, temperature, and pressure. The metering pump also offers polymer metering as well as the necessary process pressure.
Die Assembly:
The most essential element of the melt-blow process is dying assembling. Polymer-feed distribution, die nosepiece, and air manifolds are the three different components. In the case of die assembly for melt-blown, feed distribution die is a relatively tricky task than sheeting or film die.
Feed Distribution
The feed distribution is developed precisely that the polymer distribution is less reliant on the polymer’s shearing characteristics. Through a distribution system, this characteristic permits the melting of a wide range of polymeric compounds. Across the desert, feed distribution maintains a balance of flow and dwell duration.
Air Manifolds
Air compressors generate high-velocity air, supplied through slots at the upper part of the die nappies by air manifolds. To heat the air compressor to the required processing temperature, a heat exchange device, such as an electric or gas-fired furnace, is used. Through small air holes, they emerge from the top and bottom of the Dior.
Step-03: Web Formation
High-velocity hot air currents stretch the polymer streams to create microfibers as soon as the molten polymer is released from the die hole. The microfiber hot airflow is pulled in huge volumes into the ambient air as it travels towards the collection screen, cooling and solidifying the fibers. The sulfide fibers are then strewn around the collecting screen at random. Creates a self-adhesive non-woven web.
Due to airflow disruptions, the fibers are typically distributed randomly, but there is a slight bias towards the machine. The collector’s velocity and position from the die nosepiece may be adjusted to generate different forms of molten-blown web. To retract hot air and enhance the fiber laying process, a vacuum is usually supplied to the inside of the collector screen.
Step-04: Winding
Typically, the molten swelling web is wrapped on top of the cardboard core and then treated according to the finished criteria. The combination of fiber tangling and fiber-to-fiber bond formation typically results in sufficient web integration, allowing the web to be utilized quickly. These molten-blown webs can, however, be subjected to additional bonding and terminating processes.
Step-05: Bonding
Extra fiber attachment bonds and fiber tangling are used to modify web features. The most frequent approach is thermal bonding. The connection might be broad or specific. Bonding is a typical method of increasing web resistance and durability to abrasion. The web grows tighter and less like a cloth as the bond level rises.
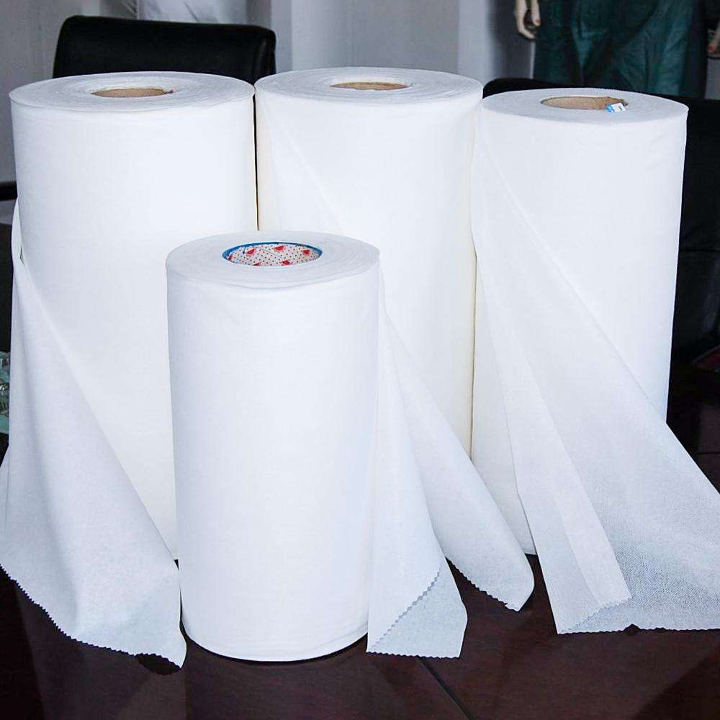
Step-06: Finishing
The majority of non-wovens are currently rolled near the end of the production line. Many people, however, use extra chemicals as well as procedures like calendaring, embossing, and flame solvents. Some of these procedures can be used at any point during the manufacturing process, while others must be applied to specific finishing activities.
Melt Blown Extrusion Process
Melt blown extrusion is a technique that employs high-velocity airflow to extend molten polymer resin from an extruded die tip or a take-up container. The procedure has evolved substantially since its inception in the 1950s. To handle and regulate the process, specifically developed melt balloon fabric extruder equipment is used. The essential components of the process are_
Resin feed system
The raw material for the smelting process is a thermoplastic resin in the form of a paste which is deposited in a resin bag and placed in an extruder hopper. The extrusion contains several different polymers for use e.g.
- PP [Polypropylene]
- PC [Polycarbonate]
- PBT [Polybutylene terephthalate]
- PA [Polyamide]
- ePP [Elastic Polypropylene]
Extruder assembly
The screw impeller of the extruder is divided into three zones: feed, conversion, and metering. The feed area of the impeller is where the material first enters the extruder and melts. The polymer feed is aggregated and compressed in the transformation area, which has a decreasing depth. Filtering any debris or molten polymer takes place at the metering zone.
Metering pump
The molten polymers are now transferred to the metering pump. A metering pump is such a kind of pump that controls the pressure, temperature, and concentration of the input by supplying a consistent quantity of clean polymer mixture to the die assembly. The output of the metering pump subsequently feeds the assembly.
Melt blown die assembly
There are three main components in the die assembly, as well as two different feed distribution options. The die nosepiece is a hollow, tapered metal component by which molten polymer will flow to produce the melt-blown fabric, and it has a tight tolerance. The air manifolds deliver hot air at high velocity to the extruded fibers exiting the die nosepiece.
Collector
As the molten polymer extends farther into the airflow, it is propelled by a high-velocity hot airflow from the air manifold, producing a microfiber. As a collector, the flow of hot air may also suck secondary air from the surrounding air, cooling and stabilizing the web of collected material. The fibers stiffen and fall on top of the collector in a random pattern, forcing the web to develop.
Winder unit
In the winder unit, the cooling fabric from the collector is wrapped onto a cardboard core. There is sufficient cohesiveness between fibers in several forms of melt blown nonwoven fabric to make the product acceptable for usage. It may be required to process the material to change its properties. When extra bonding is required, thermal bonding is a typical approach.